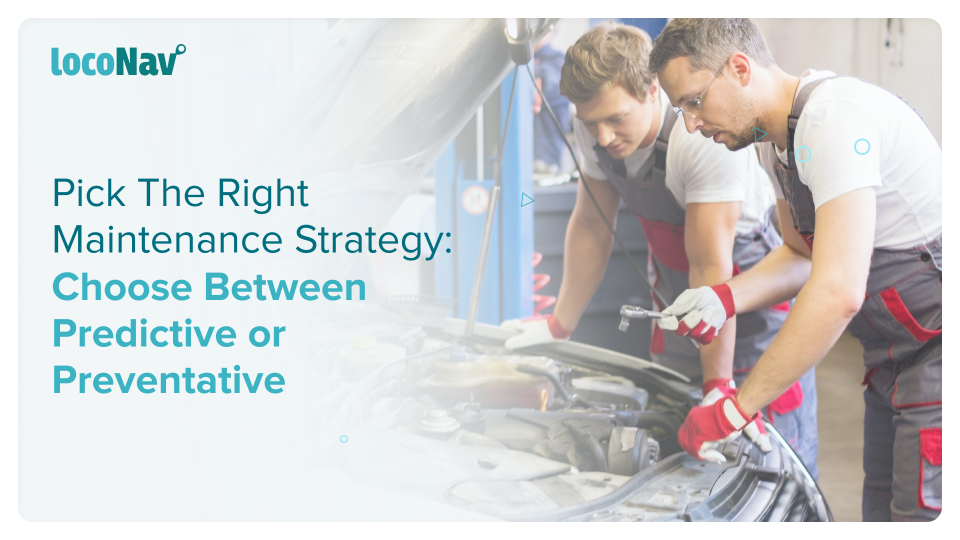
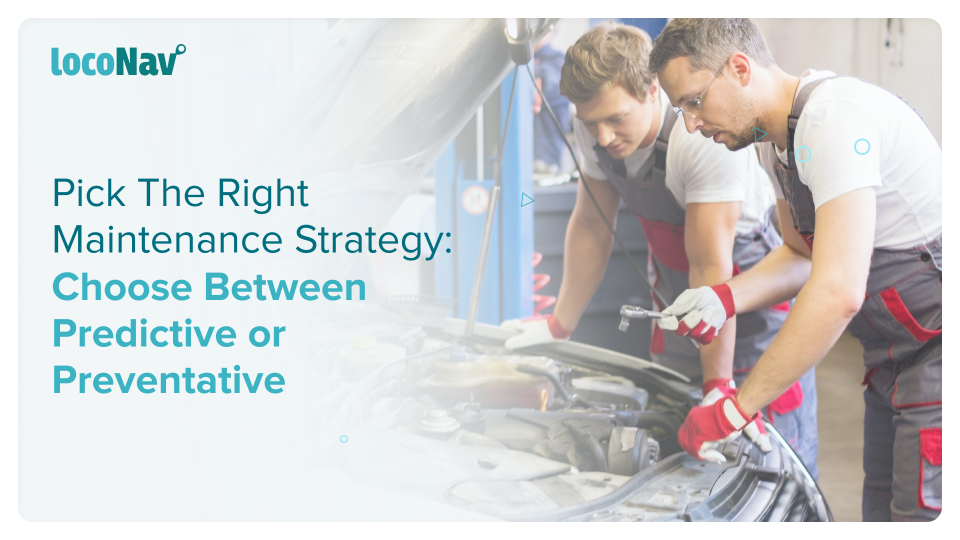
You can’t afford to rely exclusively on reactive maintenance if you want to run a successful asset management approach. The most cost-effective asset conservation techniques use both types- predictive and preventive maintenance.
These two types of maintenance strategies seek to improve asset reliability and reduce the chances of machine failure, hence lowering the high costs of unscheduled repair. However, despite having the same purpose and being complementary, preventive and predictive maintenance are not quite the same.
Manage your fleet efficiently with LocoNav’s Fleet Management Solutions!
What is predictive maintenance?
Fleet predictive maintenance is a developing area, with new alternatives for communication and data collection being developed all the time. It is a proactive strategy, similar to preventative maintenance. The primary distinction between preventive and predictive maintenance is that predictive maintenance employs condition-monitoring technology to examine asset performance in a more real-time, data-driven manner, thereby identifying possible issues before they arise.
Vehicle predictive maintenance measures machine activities as they occur and uses this data to raise red lights when signs of a problem are detected. In conclusion, predictive maintenance:
- Is proactive
- Can be carried out while the machines are in normal production mode.
- Identifies and fixes possible issues, allowing maintenance to take place before a breakdown occurs.
- Relies on networked measurement and data gathering systems, as well as tools and employees for data analysis
What is preventive maintenance?
Vehicle preventive maintenance is a sort of maintenance that is performed on pre-determined assets on a cyclical basis in order to optimize their working conditions. The maintenance crew can change parts and make modifications before any signs of trouble arise with regular technical tests. This proactive maintenance method assists businesses in avoiding equipment failure, machine downtime, and, of course, extending the life of assets.
Consider preventative work to be similar to physical medical examinations. Maintenance personnel set up vehicle preventative maintenance work to prevent fleet breakdown and optimize its operating conditions, just as doctors advise some patients to have health checks to prevent illness and improve their quality of life.
What is the difference between predictive and preventative maintenance?
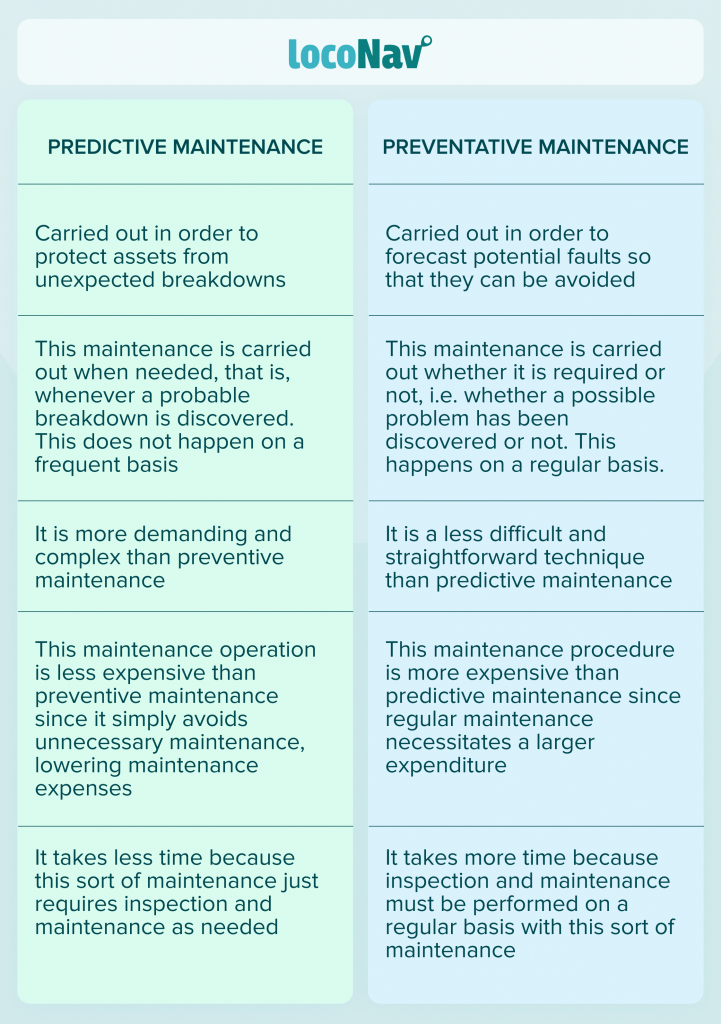
How to use predictive analysis in vehicle management?
Predictive analytics is a strong and comprehensive tool that assists users in making educated future decisions by leveraging known data to forecast future occurrences. To achieve these goals, it employs a variety of approaches, including data mining, statistical modeling, and machine learning.
This is how it can be used to improve vehicle management effectiveness:
Predictive Asset Maintenance
The industrial predictive analysis could potentially be used to track the health of vehicles and enhance maintenance standards. Data generated by sensors installed throughout the vehicle can be fed into models designed to identify early warning indications that can lead to part failures, mechanical breakdowns, and decreased fuel efficiency.
The results can disclose which vehicles or parts are the most prone to failure, how frequently vehicles must be hauled in for regular maintenance, and whether parts supplies are adequately stocked. The most sophisticated models can even forecast component failures before they occur.
Long-term, this degree of understanding could assist fleet managers in extending the lives of their vehicles while decreasing downtime and its associated costs, such as overloaded service facilities, lost work hours, and nondelivery charges.
Customized Safety Education
Industrial predictive analytics could assist the design of safety training programs tailored to analyze and improve performance in crucial areas, boosting safety scores for individual workers and the company as a whole by providing fleet managers with specific information about each employee’s driving performance.
LocoNav fleet management software helps track and enhance fleet maintenance, from studying individual driver behavior to telling your maintenance personnel ahead of time the spare parts they may require.
LocoNav allows fleet managers to concurrently examine engine performance indicators, record speeding drivers, and monitor the temperatures of chilled assets. Their fleets function more safely and efficiently as a result of past fleet performance data and real-time emergency notifications.
FAQ
What is an example of predictive maintenance?
Vibration analysis, oil analysis, thermal imaging, and equipment monitoring are some applications of predictive maintenance and predictive maintenance sensors.
What type of challenges are catered to by preventive maintenance services?
- Building maintenance into your schedule can help reduce downtime significantly caused by maintenance problems.
- Preventive maintenance will reduce the number of unexpected surprises that damage your productivity and profitability.
- Preventative software can increase asset management and machinery longevity
What is a preventative maintenance checklist?
Preventive checks for machines:
- Before and after each shift, ensure that the machinery is free of debris.
- Every day, clean the machine surfaces of grease, dirt, and other loose particles.
- Inspect tools for sharpness on a regular basis.
- Examine and replace any worn or broken instruments.
- Check and replace all machinery fluid levels and air filters on a regular basis.
- Regularly calibrate machines.
How to balance preventive & predictive maintenance for fleet optimization?
Choosing a fleet maintenance system can boost profitability and ROI. Both approaches to maintenance have the same goal: to predict and avoid vehicle breakdown over the life of the vehicle asset.