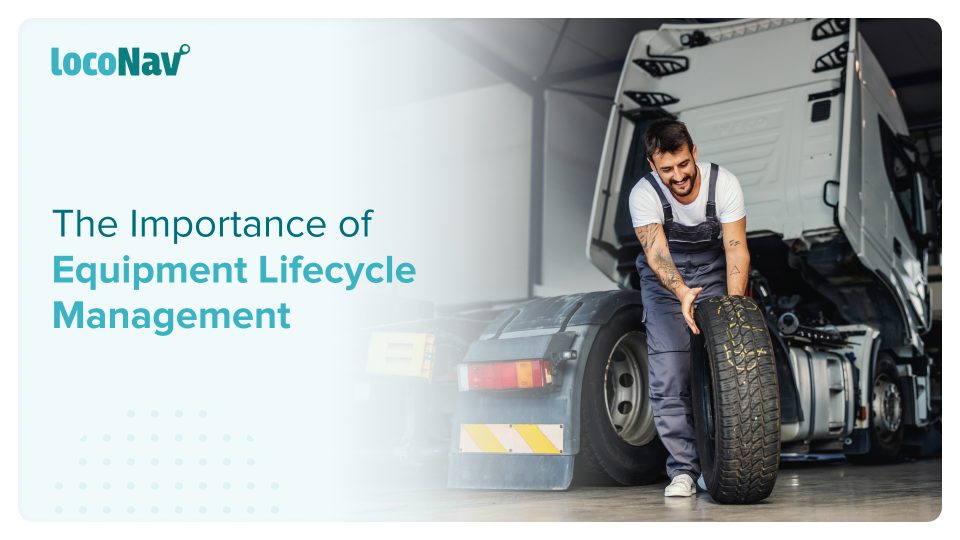
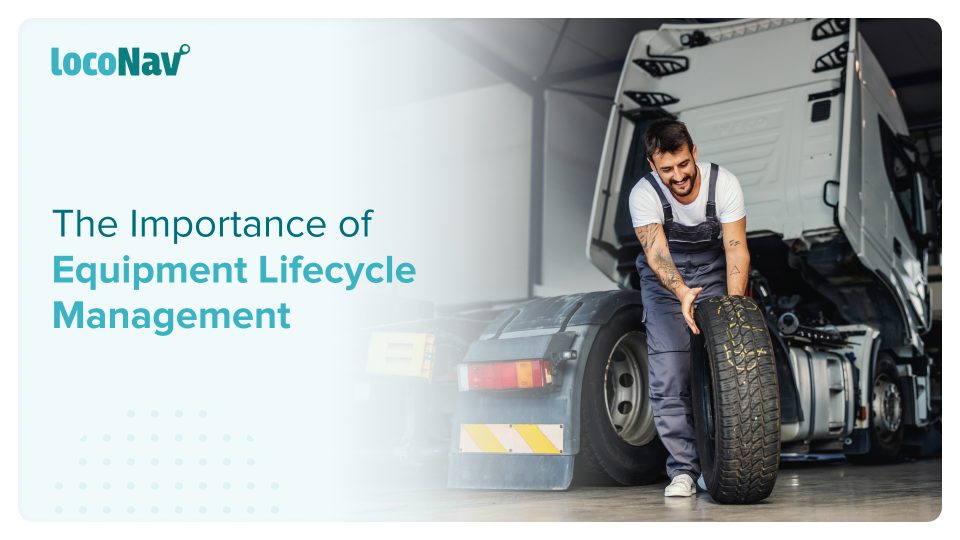
Replacing vehicles and equipment at the right time benefits your business’s overall productivity, efficiency, and profitability. Effective asset lifecycle management strategies can also help to reduce overall corporate expenditures.
However, decisions on vehicle and equipment lifecycle management are rarely as easy or straightforward as purchasing or leasing equipment for a defined period of time. Such judgments necessitate the capacity to assess where an asset is in its lifetime and to determine the steps that must be taken to manage expenses and decrease risk.
What is Equipment Lifecycle Management?
Equipment lifecycle management is critical to running a small business fleet profitably. Many small fleet owners and managers have a notion of when it is time to replace a vehicle based on its age and mileage. However, there are additional crucial elements to consider while maximising equipment lifecycle management.
Staying in the comfort zone of lowering capital expenses is frequently the most expensive choice during the lifecycle of a vehicle. Equipment lifecycle management must encompass more than just the vehicle’s original purchase price to account for all of a vehicle’s entire operational costs.
Manage your fleet efficiently with LocoNav’s Fleet Management Solutions!
What is the Lifecycle of an Asset?
Every asset, such as a vehicle, has an optimal working life during which it performs optimally. Wear and tear will lower this after a period of use. And once an asset reaches this stage, the cost of upkeep and repairs can quickly outweigh the cost of replacement.
The end of an asset’s lifecycle might vary according to a variety of factors, including the amount of usage, how it was used by a driver or operator, the robustness of the maintenance plan, and even the operating conditions. An asset that outperforms a comparable asset may approach the end of its lifecycle sooner and require replacement at more frequent intervals.
How Does Managing Asset Lifecycle Increase Productivity?
There are several advantages to establishing a solid equipment lifecycle management strategy in your fleet. Here are 4 ways your fleet might benefit from asset life cycle data.
- Define your assets and their associated conditions
With the correct asset management software, you can keep track of the installation date, condition, and cost-effectiveness of any piece of equipment. This information can be used to evaluate an asset’s useful life and total cost of ownership.
- Proactive Maintenance
Equipment lifecycle management enables a company to actively control the physical health of its equipment. Proactive maintenance allows organisations to better forecast future events, plan for asset failure, and conduct well-planned maintenance and replacement measures.
- Regulatory Assistance
Your team may collect and use vital life cycle data for each essential asset with the help of building infrastructure management software. In this manner, your team is aware of current issues before they become regulatory compliance issues.
- Vehicle Replacements
Creating and maintaining a capital budget is an essential component of fleet management. Your team can more correctly predict finance needs and guarantee adequate maintenance reserves by staying up to speed on asset status and life expectancies.
What are the Stages of Equipment Lifecycle Management Planning?
Throughout its existence, each asset goes through five major stages: plan, acquire, utilise, maintain, and dispose of. The majority of your time will be spent in the usage and maintenance stages, but each stage is equally vital in ensuring you get the most out of your equipment.
- Planning
The planning of the equipment lifecycle management stage begins with recognising that a requirement in your institution is currently unmet. You are planning when you start brainstorming and researching items that might address your challenge.
- Acquiring
When you have located the ideal asset to match your facility’s requirements, the next step is to acquire it. Acquiring an asset entails not only purchasing it but also transporting it to your location.
When you acquire a new vehicle, there is a lot of paperwork that comes with it and needs to be stored properly. Using the LocoNav “Documents” tab, you can keep all your documents in one place for safekeeping and easy access.
- Utilising
You can start using the new asset now that it has arrived at your facility! Once it is up and running, review the asset’s requirements and how your team can effectively care for it.
- Maintenance
After you have created a service management plan for the asset, utilise it normally until maintenance is required. Perform the required maintenance to get your asset up and running again, whether it is a time-based, meter-based, or condition-based trigger.
You can maintain all maintenance-related paperwork in the LocoNav “Maintenance” tab. You can also set alerts to remind you of periodic maintenance. Vehicle maintenance can also be decided on the basis of LocoNav’s vehicle scorecard.
- Disposal
Additional upkeep will no longer be a financially feasible decision at some point, and disposal will be the best option.
What Factors Impact Asset Lifecycle Planning?
An asset’s lifecycle planning is affected by the following factors:
- The assets needed by the fleet owner, manager, operator, and driver
- How the vehicle is used
- Where the vehicle is usually operated (terrain, weather conditions)
- Vehicle features and capabilities
- Vehicle’s maintenance plan
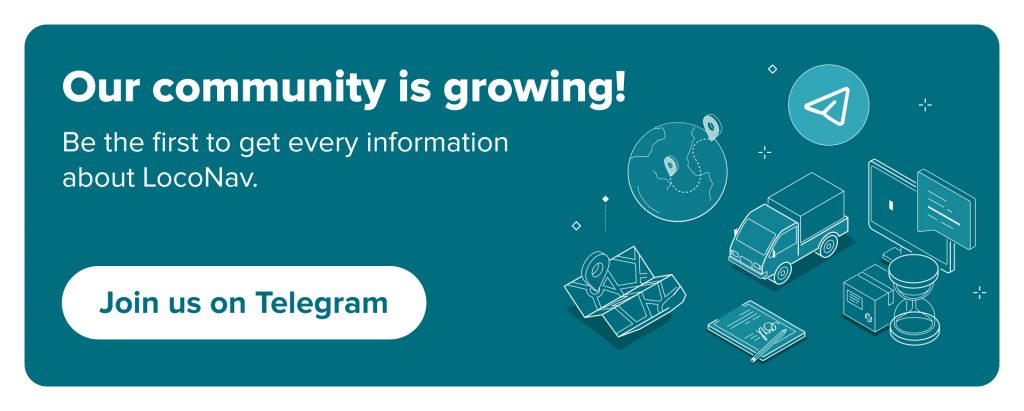