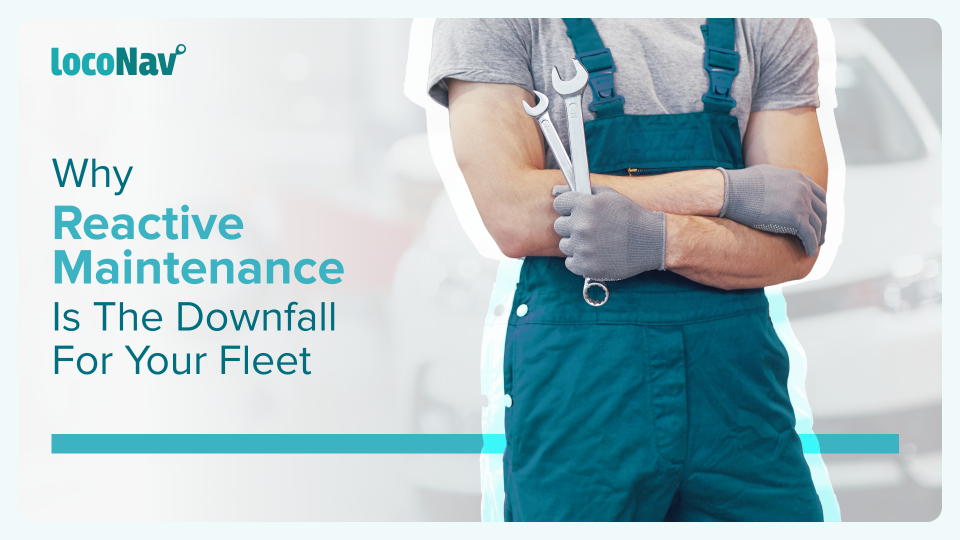
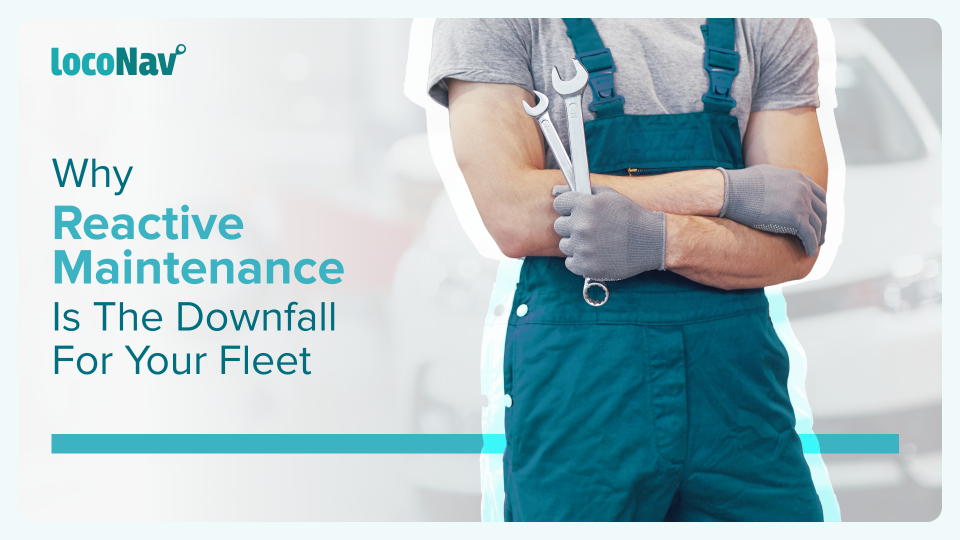
Logistics is an asset-heavy industry and the demand for reliability and availability of equipment in such an industry is massive. To keep up with this demand, you must choose the perfect maintenance approach. To meet manufacturing needs, keep up with competitors, and maintain growth statistics, companies need an effective maintenance program to keep machines and equipment running.
What is Reactive Maintenance?
Reactive maintenance, also known as breakdown or repair maintenance, is a strategy to return equipment to its normal operating condition only if it fails, which means that routine repairs or maintenance are not performed. Plan to reduce the number of incidents.
The drawbacks of reactive maintenance vastly outweigh its benefits, but it does have some advantages under the right circumstances. For example, you might have an asset that has low repair costs and is not required to operate, or you already have a plan to replace your machine from time to time, making preventive maintenance unnecessary.
With a minimum of maintenance personnel and fewer repair costs, reactive maintenance can be a cost-effective approach initially, but should not be your long-term strategy.
Manage your fleet efficiently with LocoNav’s Fleet Management Solutions!
Why Is Reactive Maintenance The Downfall Of Your Fleet?
Assets Have A Shorter Life Span
Reactive maintenance constitutes only scheduling repairs once a piece of equipment has failed. Reactive maintenance does not keep the system in optimal conditions. Over time, the quality of the maintained systems will degrade faster due to the associated failures and therefore will not maximize your initial capital investment. This negatively affects the RONA (return on net assets) of the company, thereby lowering the value for shareholders.
Longer Equipment Downtime
Scheduled maintenance can be accounted for in the production schedule, and unscheduled repairs can occur at any time. In addition, there is ambiguity about the length of the delay due to unplanned repairs. Equipment failure often / infrequently reduces reliability between service and production.
Incompetent Resource Management
Technicians spend valuable time searching for the right manuals and diagrams, ordering the right parts, and more trying to diagnose and fix the problem. Often they need to wait for the license and device license to be received. Payment for your resources (equipment, special tools, equipment, etc.) is much higher for last-minute problems.
Collateral Damage
A small problem can quickly turn into a major system fix. For example, if your car is low on engine oil, it can lead to a cylinder malfunction or seal damage warning, but in the end, a completely stuck engine or slight shaft misalignment not only damages the bearing but can lead to cracking over time. The gearbox also stands to get jammed or even the shaft itself can be damaged.
Scheduled Preventive Maintenance Disrupted
Emergency repairs are often preferable to routine maintenance. Scheduled work can be delayed or canceled altogether, resulting in unexpected disruptions along the way to unplanned overtime and loss of future backup work. This is what is known as the death spiral.
Disheveled Budget Allocation
Because equipment failure can be unpredictable, manpower and parts may not be available, so organizations may have to pay surcharges for urgent parts delivery, travel time, and out-of-hours support. Full forecast of when the budget will be spent.
Unplanned downtime can delay orders if equipment cannot be returned to production in time. This can damage your reputation and affect your income. Acquiring solutions from unregistered vendors can cost the organization millions of dollars.
Increased Safety Effects
When a maintenance job is properly planned, technicians have time to learn standard procedures and safety requirements to get the job done correctly. Technicians tend to take more risk when maintenance is reactive because they are forced to get systems up and running without delay. Wellness is one of their strategic goals and the reactive/disruptive approach goes against that.
Timely repair of damaged equipment is critical to minimizing downtime. Therefore, using a reactive maintenance strategy is in most cases an inefficient and very expensive way of working. The cost of emergency repair is 5-7 times higher than the planned cost of emergency work can have a big impact on profitability.
Routine and periodic maintenance results in improved asset reliability and availability, improved reporting and metering, improved efficiency across all sources, and lower overall maintenance costs. This is in part due to fewer urgent repairs, calls from suppliers, necessary spare parts, material rationalization, and reduced productivity. Responsive maintenance is more expensive because it is impossible to adequately plan the cost of the resources required. In addition, it should be borne in mind that routine maintenance can prevent failures.