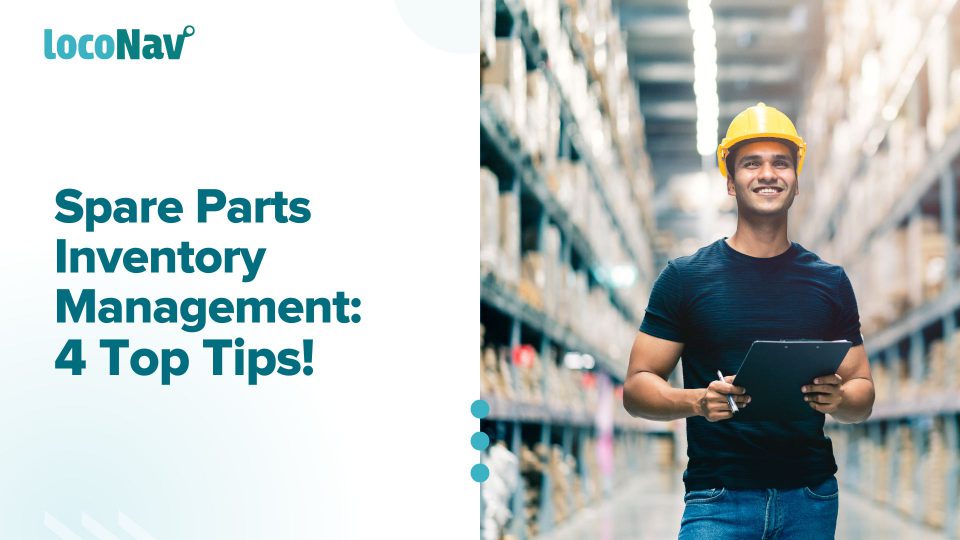
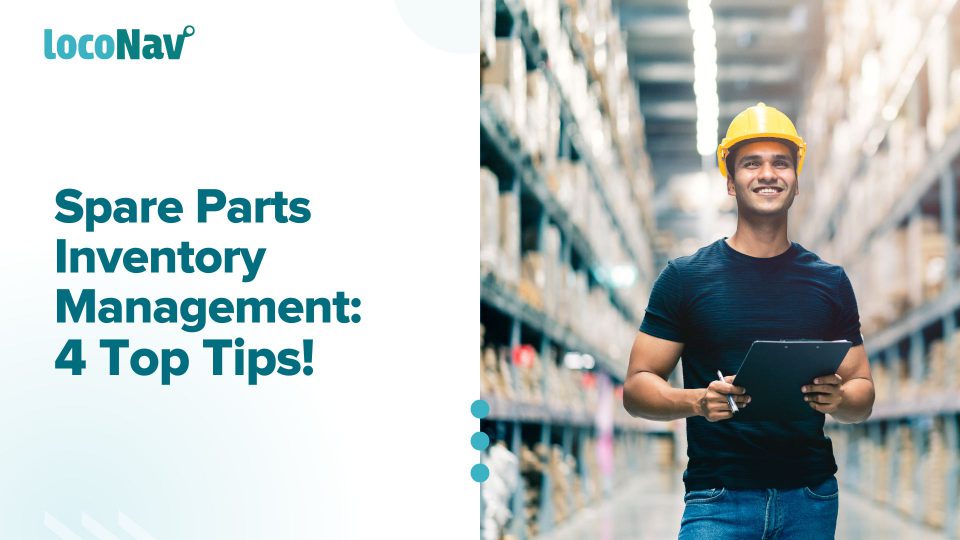
Parts are in low supply in the transportation business. Although for telematics, the low supply began with the global microchip shortage, it is now spreading into the aftermarket, with fleets reporting wait times for replacement parts required to complete maintenance service or repairs.
Parts management is essential for fleet operations. Spare parts must be available when parts need to be replaced; yet, retaining too many spare parts will raise inventory and costs. In this blog, we will discuss types of fleet spare parts and how spare parts inventory management can help you elevate your fleet operations.
Types of Spare Parts
Spare parts can be broadly classified into 4 categories:
- CAPITAL SPARES are crucial parts that are typically replaced during equipment capital repairs. As a result, the procurement activity and delivery of these supplies must be organised at the time the equipment is picked up for capital repair.
- OVERHAUL SPARES are parts that must be changed each time the vehicle is disassembled and reassembled.
- WEAR AND TEAR SPARES are parts that experience regular wear and tear during equipment operation and must be changed after a certain number of hours of operation.
- CONSUMABLE SPARES are items that are often utilised, such as fasteners, seals, gaskets, and fuses. These are typically low-priced things.
Manage your fleet efficiently with LocoNav’s Fleet Management Solutions!
Benefits of Managing Your Spare Parts Inventory
It is indisputable that SaaS continues to make fleet management easier. The benefits grow when fleets integrate more and more of their processes into a single software system. Some of the advantages of adopting the software for spare parts inventory management are as follows:
- Elimination of time-consuming manual data entry
- Eradication of errors frequently associated with manual records
- Simple synchronisation across several locations.
- Continuous tally of parts inventory levels and expenses automatically.
- Overstocking is avoided, and the budgets for spare parts are reduced.
- Data can be updated and accessed from any location.
Best Practices for Spare Parts Inventory Management
The following best practices will guarantee that your spare parts inventory management system runs smoothly:
#1 Regular Counting
It’s critical to check inventory levels on a frequent basis, which for many means on a daily or weekly basis. Make that your inventory is the same number, location, and part type as it is in your spare parts inventory management system.
Additionally, conduct random fleet inventory audits to confirm that your physical counts or stock correspond to your financial records. Expense management is just as crucial as spare parts inventory management.
#2 Classification System
When choosing the number of replacement parts to have on hand, prioritise your fleet’s inventory. This will assist you in determining how frequently various parts need to be refilled. This will help you in categorising the most crucial assets and improving spare parts inventory management.
#3 Reporting and Forecasting
Examining your fleet’s reports and historical data can assist in providing the necessary inventory information. Tracking how long parts normally survive, which brands perform best, and how frequently components require maintenance can help you decide how frequently to refill your inventory.
Reports can also be used to calculate how much downtime a piece of equipment would experience if a specific part was out of stock and needed to be repurchased. This might help you determine how many spares to have on hand. If you do need to refill a part, recognising its importance will help you determine which parts require expedited shipping and which can wait for ordinary delivery services.
#4 Preventive Maintenance
Regular preventive maintenance on your equipment can disclose the status of parts. This will assist you in identifying parts that will need to be changed soon, providing you time to ensure the part is in stock or order a replacement if necessary. During preventive maintenance, parts can also be fixed or scheduled for additional service sessions.
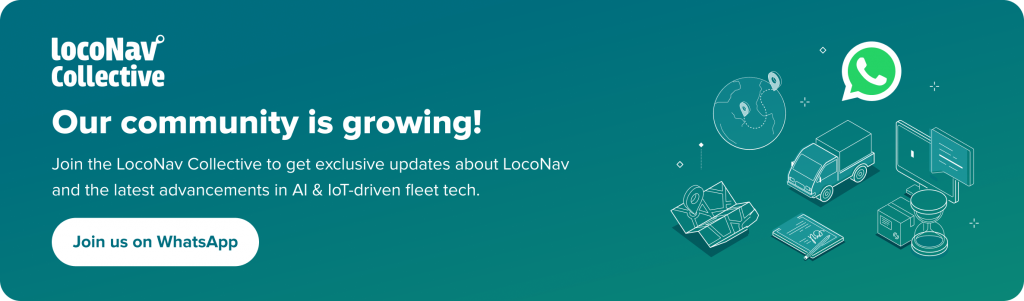