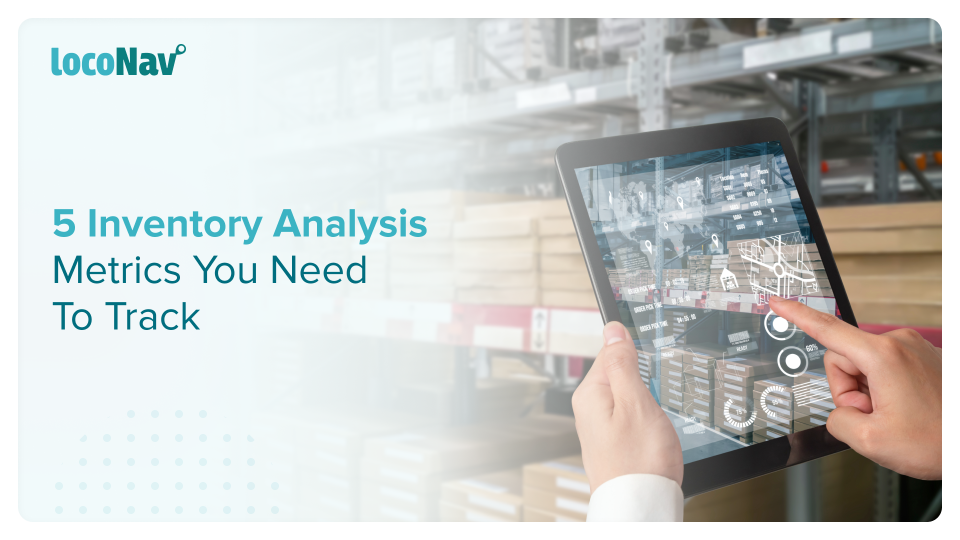
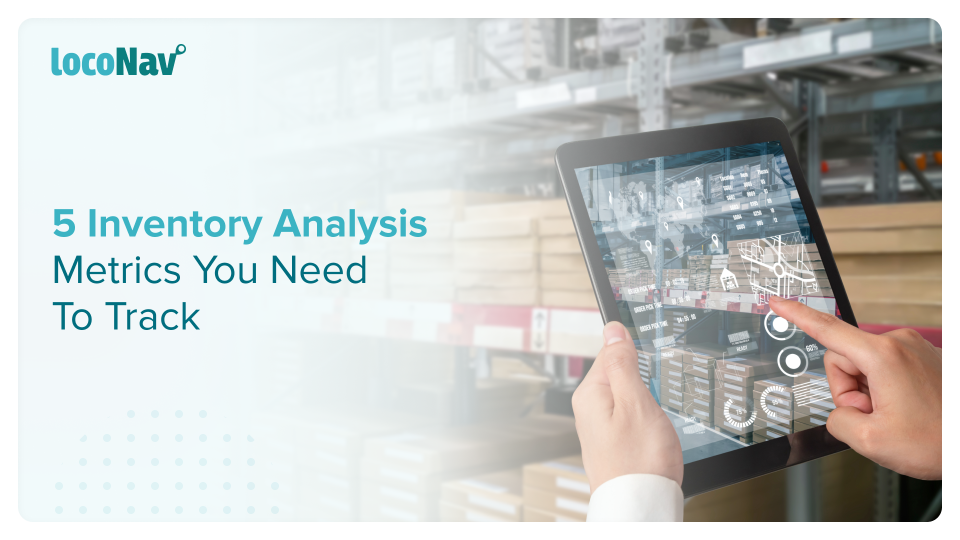
If you are in the contracting business and own a fleet of service vehicles, how can you determine whether your truck inventory is doing well?
Inventory Analysis Metrics help you track, quantify, and evaluate your service vehicle’s performance and can be the deciding factor for your productivity and profitability. Contractors can use inventory analysis metrics for:
- Identifying areas of improvement
- Determining accurate inventory levels by comparing them to historical data
- Comparing themselves with competitor service fleets
It is an important practice for contracting businesses to track their key metrics for every aspect of their business. This includes customer satisfaction, inventory, financial performance, supply chain, and more. In this blog, we will discuss the role of inventory analysis in fleet management and inventory analysis metrics that can impact your business.
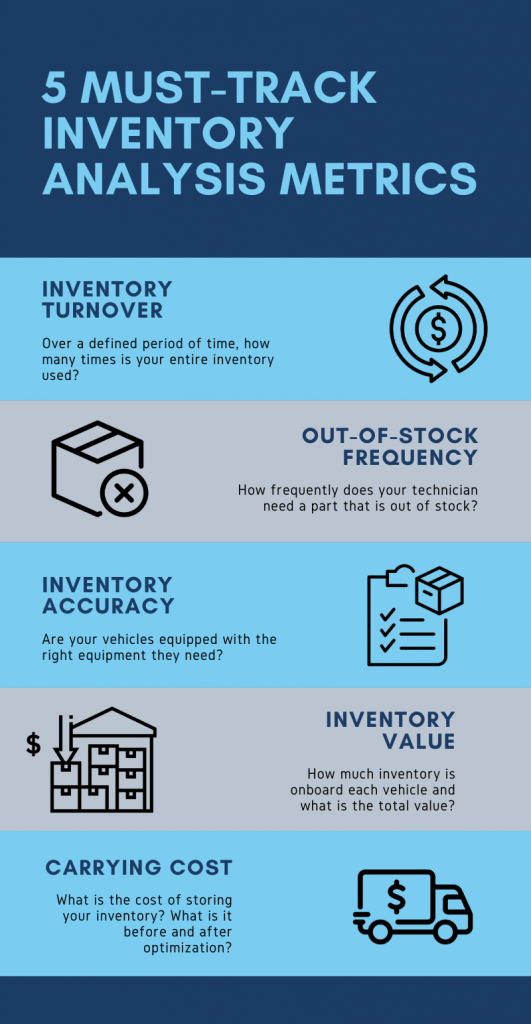
Manage your fleet efficiently with LocoNav’s Fleet Management Solutions!
What is Inventory Analysis in Fleet Management?
Inventory analysis in fleet management is the practice of using data points to boost overall inventory efficiency. In inventory analysis:
- Metrics are evaluated against historical data to set industry benchmarks and identify areas of improvement.
- Cash flow is improved by determining accurate inventory levels and preventing the investment of too much capital into stock.
- Resources are optimally used and inventory shrinkage caused due to damage, loss, and theft is minimized.
Impact of Poor Inventory Analysis on Your Fleet
Tracking the correct inventory data ensures that the inventory levels in your service trucks are optimum. This allows you to avoid the following costly issues:
- Over-Purchasing Inventory: Keeping inventory on hand “just in case” has a negative impact on cash flow and affects profitability in a low-margin economy. The additional storage costs add up as well.
- Inadequate Visibility: An inefficient inventory monitoring and restocking system do not provide the clarity essential for projects, making the technician’s task that much more difficult. Inaccuracies multiply if the data does not flow to your accounting system.
- Inefficiency: You avoid waste, enhance the utilisation of your technician’s time and resources, get more work accomplished in a day, and please clients by ensuring each truck is equipped with what is needed for each job.
- Customer Dissatisfaction: If your contractor has to stop working on a job because a vital part is missing, it is not only a costly problem (wasted time, gasoline costs to obtain the missing item, extra truck wear and tear), but it also increases customer displeasure. This can result in lost business.
- Missed Opportunities: If you are not measuring the correct metrics, you can lose out on prospects because you do not have a vital item on hand.
5 Must-Track Inventory Analysis Metrics
Contractors often make the mistake of not evaluating all the important inventory analysis metrics. This can result in over or under-stocked inventory. While choosing the key inventory analysis metrics, here is what you should consider:
- Identify things that worked in the past
- Choose metrics that align with your business goals
- Do not overlook customer satisfaction metrics
- Monitor historical data to determine operational gaps
Based on these considerations, contractors should measure the following inventory analysis metrics:
- Inventory Turnover
Over a defined period of time, how many times is your entire inventory used?
- Out of Stock Frequency
How frequently does your technician need a part that is out of stock?
- Inventory Accuracy
Are your vehicles equipped with the right equipment they need?
- Inventory Value
How much inventory is onboard each vehicle and what is the total value?
- Carrying Cost
What is the cost of storing your inventory? What is it before and after optimization?
Final Thoughts
Contractors and their vendors make frequent errors when it comes to tracking their performance. Many suppliers, for example, rely only on past data to estimate how much and when to restock an item. But as we have seen in recent years, demand can vary dramatically. Based on historical data rather than real-time utilisation estimates, contractors may end up with too much or too little inventory. Using the correct inventory analysis metrics can help you achieve the much-coveted inventory management optimization that every fleet needs.
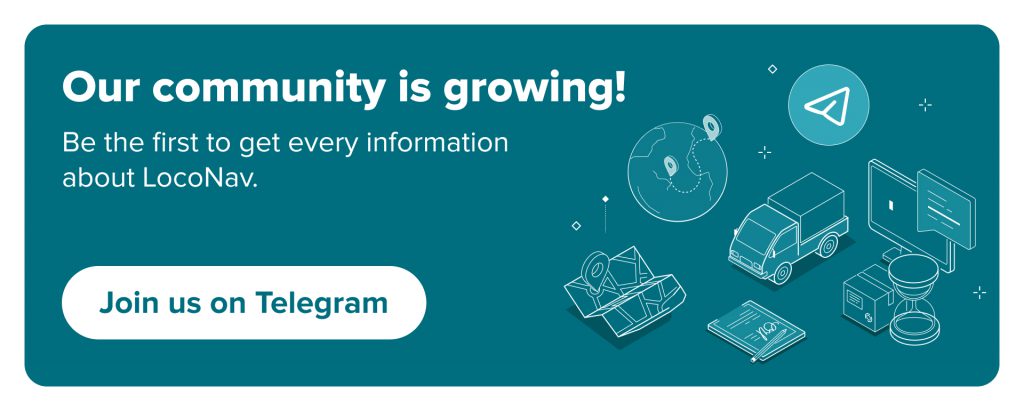